The term ‘ceramics’ encompasses all objects formed from wet clay which are hardened by firing them in a kiln. Differences in material composition and firing conditions lead to different types of end products.
Based on the chemical composition of the clay and the firing temperatures, three categories of ceramics are distinguished: earthenware, stoneware and porcelain. In general, the higher the firing temperature, the less porous (and thus less absorbent) and the sturdier the final product. But not every clay mixture can be fired at the same temperature.
Earthenware has a porous (moisture-permeable) ‘shard’ (the clay body) that is often brown, red or yellowish in colour. It is fired at a temperature between 800°C and 1100°C. The world’s oldest ceramic objects – such as Neolithic storage jars (fig. 1) – are earthenware, and were fired in relatively simple kilns or even on an open fire.
Stoneware is much harder and more compact than earthenware and almost impermeable. It is fired at a temperature of between 1200°C and 1300°C. Teapots from Yixing are a well-known example of stoneware.
Porcelain is non-porous: if a porcelain object breaks, the shards can be glued back together seamlessly. The raw materials that form the material (porcelain stone and kaolin clay, see below) are fired at an extraordinarily high temperature (1200°C-1450°C), causing them to vitrify (fuse into a glass-like substance). The shard is hard, thin, white, and slightly translucent. It also produces a bright sound when tapped – even chimes have been made of porcelain (fig. 2).
The distinction between stoneware and porcelain is a Western contrivance. In China, only two types of ceramics are distinguished: ci 瓷 (high-fired = stoneware and porcelain) and tao 陶 (low-fired = earthenware). Porcelain – which according to the Western definition should be slightly translucent – is the result of centuries of technological development, which is why Western publications sometimes still use the term ‘porcellaneous stoneware’ to describe borderline cases. The first porcelain was produced in China around the seventh century CE (depending on which definition is used). By the twelfth century, porcelain could also be made in Korea, from the seventeenth century in Japan, and by the eighteenth century in Europe. Over the centuries, attempts were made to imitate porcelain in numerous places around the world, but due to a lack of the (knowledge of) essential raw materials (porcelain stone and kaolin clay), these ceramics did not have the same qualities as porcelain. The well-known Delftware, for example, is earthenware covered with a layer of white tin glaze to make it look more like the white, glassy porcelain.
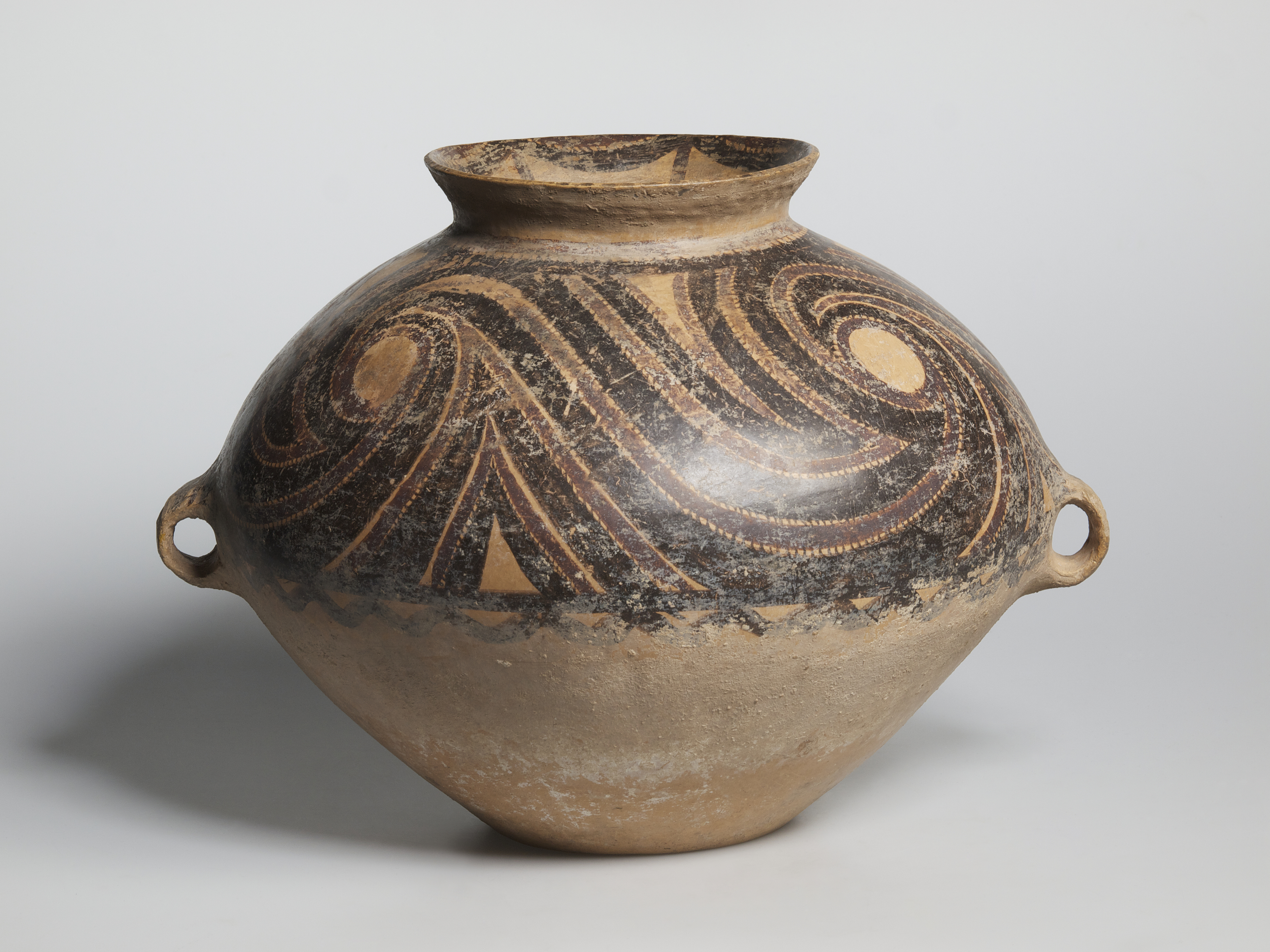
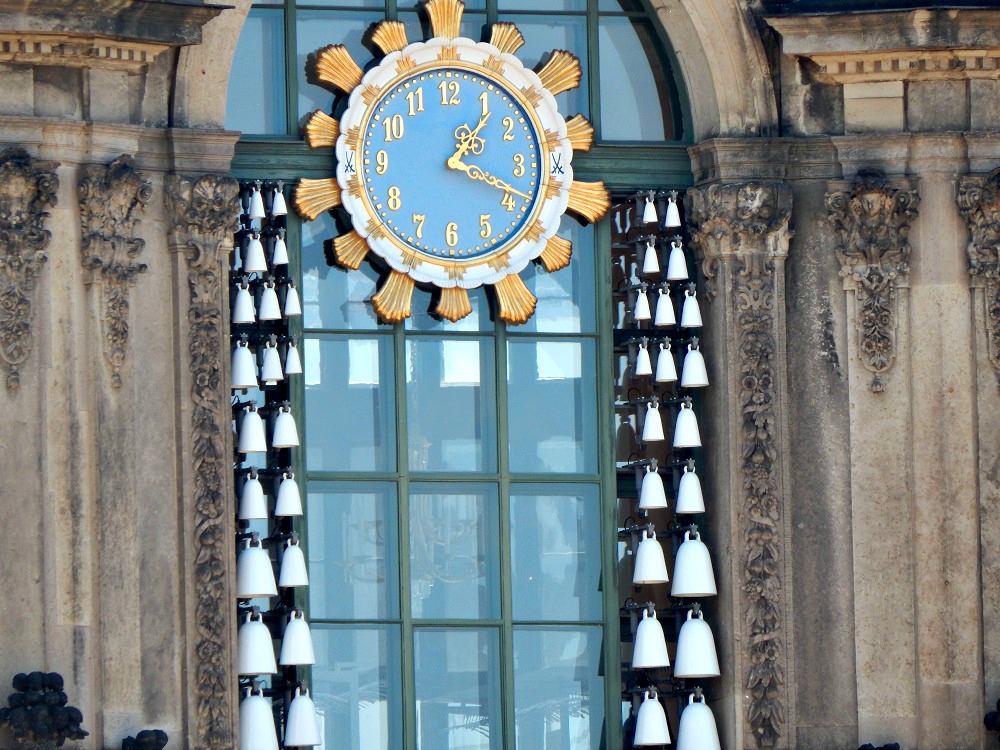
Variables affecting the final product
1) Clay
The type of clay (its chemical composition) determines what you can do with it: whether you can form large or small objects, whether it has a thick or thin wall, what colour the shard is, at what temperature you can fire it, and what kind of glaze you can apply to it.
The difference between mud and clay lies in its workability or ‘plasticity’. Unlike sand or mud, clay has the specific properties required for making ceramics, namely that you can shape it and that this shape is retained during firing.
Preparation and plasticity
Before making ceramics, the clay is often first thoroughly washed, sieved and kneaded: it must be a homogeneous mass without impurities or air bubbles, which can cause aberrations during firing. The ideal clay is a combination of plastic and non-plastic clay: plastic so that it is flexible enough to mould, non-plastic so that it is firm enough to retain its shape in the kiln. Clay can be mixed to create a certain degree of plasticity that is ideal for manufacturing the final product. A good example is the mixing of porcelain stone with the white, plastic clay called kaolin to produce porcelain, which happened mainly around the Southern Chinese city of Jingdezhen, an area where these raw materials were abundant. Porcelain stone – also known as petuntse (a corruption of baidunzi 白墩子 meaning something like ‘white bricks’) – is, like kaolin (also called porcelain clay), formed from weathered granite. So they have the same origin, but consist of a slightly different combination of minerals. As a result, porcelain stone is not as plastic as porcelain clay, but by adding the clay to the ground stone, it can be made more plastic. In contrast, for figures made in Dehua (fig. 3) (so-called Blanc de chine), clay is used that consists only of porcelain stone, and is therefore relatively non-plastic. It is thus difficult to shape anything with it – perhaps a small, thick-walled pot on a potter’s wheel – but it retains its shape very well, so will not collapse during firing. Clay such as this is ideal to press into moulds in order to make complex shapes such as the hands with thin fingers of Blanc de chine figures. Large vases, pots and bowls made of porcelain could only be produced from the fourteenth century onwards, when people switched from the ‘mono-recipe’ (clay consisting of porcelain stone only) to a ‘dual-recipe’ (a combination of porcelain stone and porcelain clay/kaolin): this made the clay plastic enough to make much larger objects.
2) Firing temperature
Firing transforms the clay into ceramics: all the water evaporates from the clay and the minerals in the clay fuse together. Certain clays such as kaolin (porcelain clay) can be fired at a very high temperature (c. 1400°C), so that it actually vitrifies. This glass-like structure is characteristic of porcelain and distinguishes it from earthenware and stoneware.
The rate at which the kiln heats and cools also affects what kind of ceramics you can make with it. Celadon (stoneware with a greenish glaze), for example, had to be made in so-called tunnel kilns, because they could heat up and cool down again quickly, which gave the glaze its characteristic greenish colour (fig. 4).
The firing temperature also determines the kind of pigments that can be used. Cobalt and copper, for example, can be fired at high temperatures, making them suitable for underglaze decoration (fig. 5) on porcelain, as they and the object can then be fired at 1400°C simultaneously. Other pigments burn away at high temperatures. In the case of porcelain, such pigments can only be applied after the first firing (at 1400°C) as an overglaze decoration, after which the object has to be fired again at a lower temperature, one that the pigment can withstand.
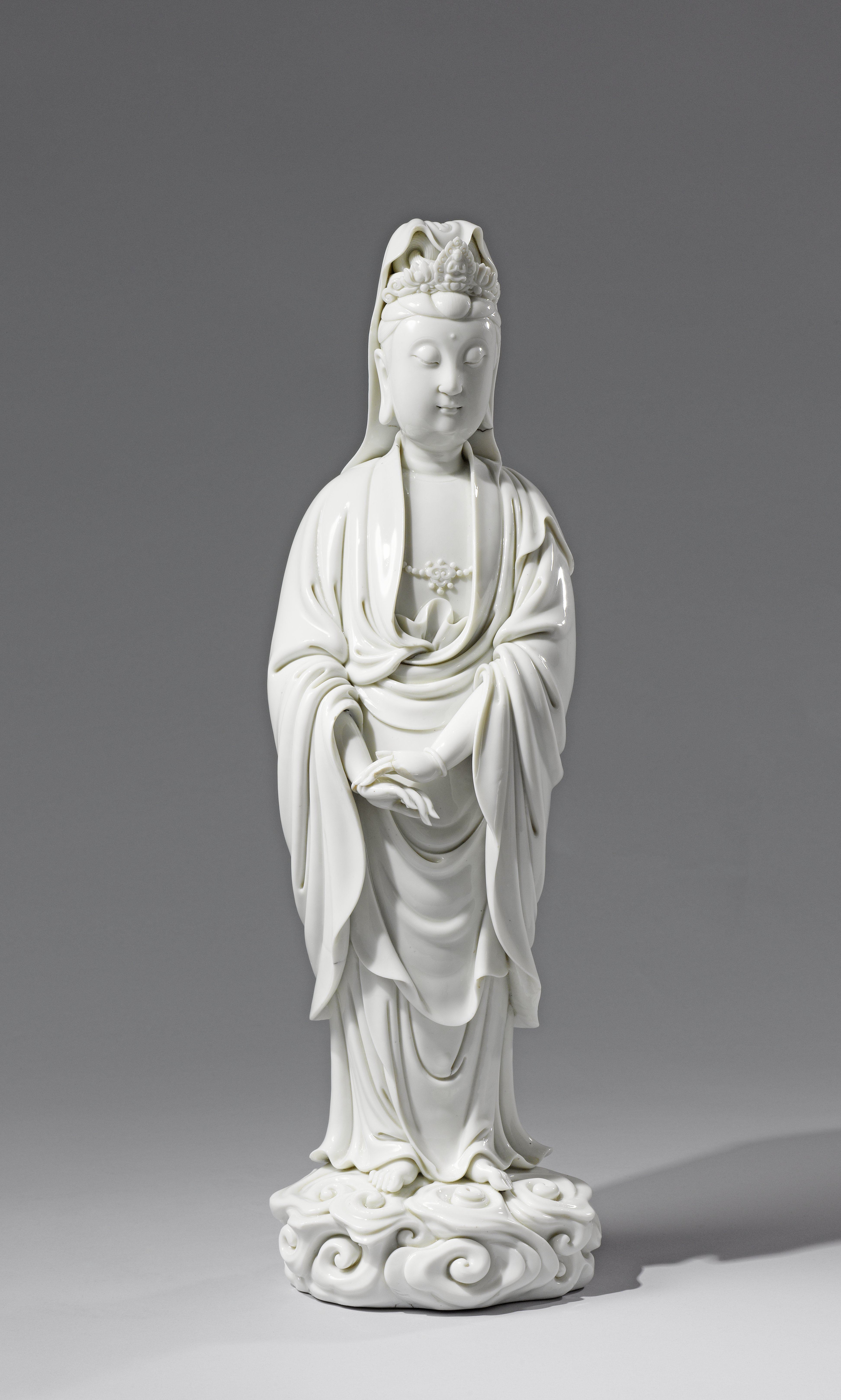
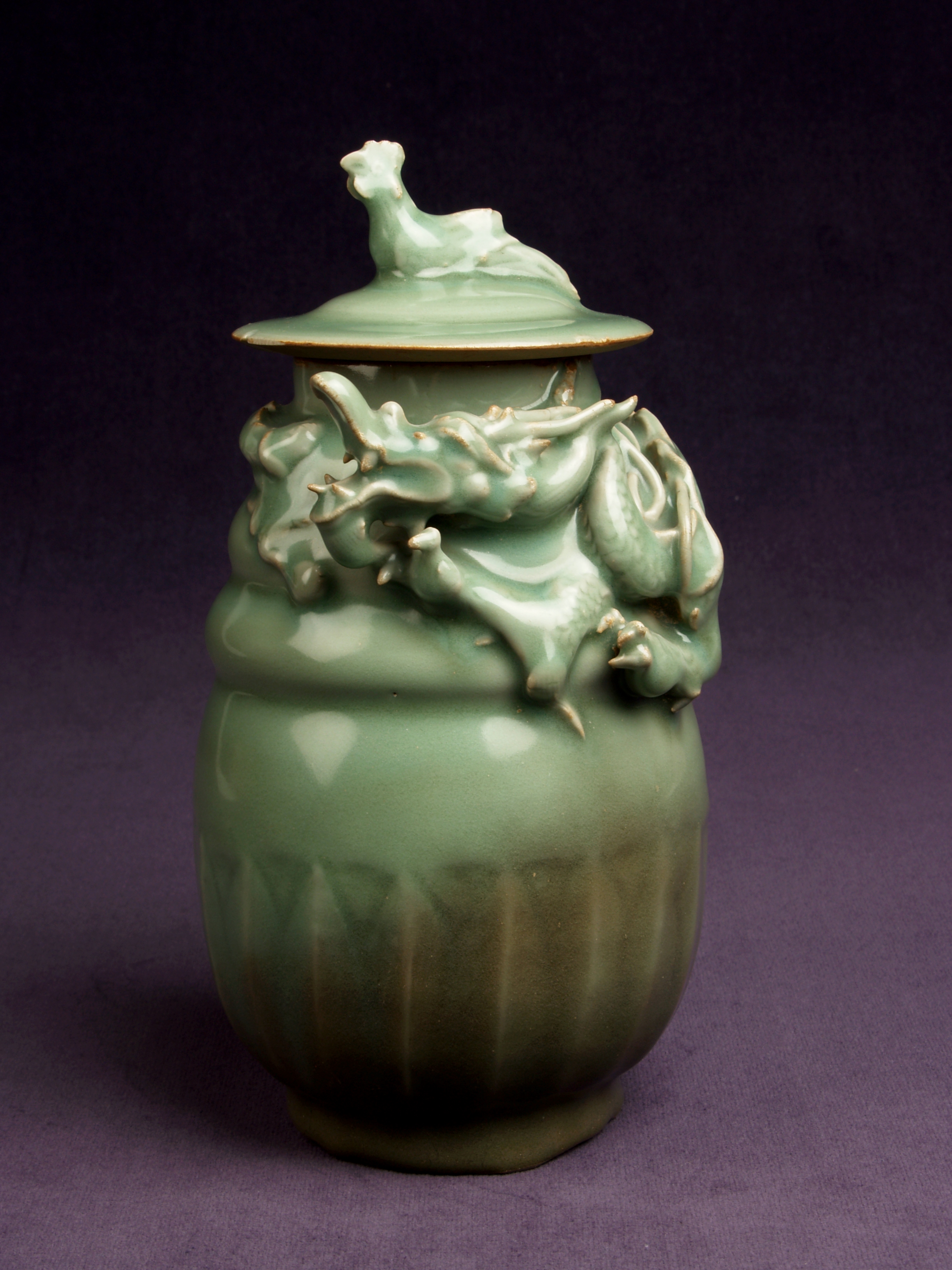
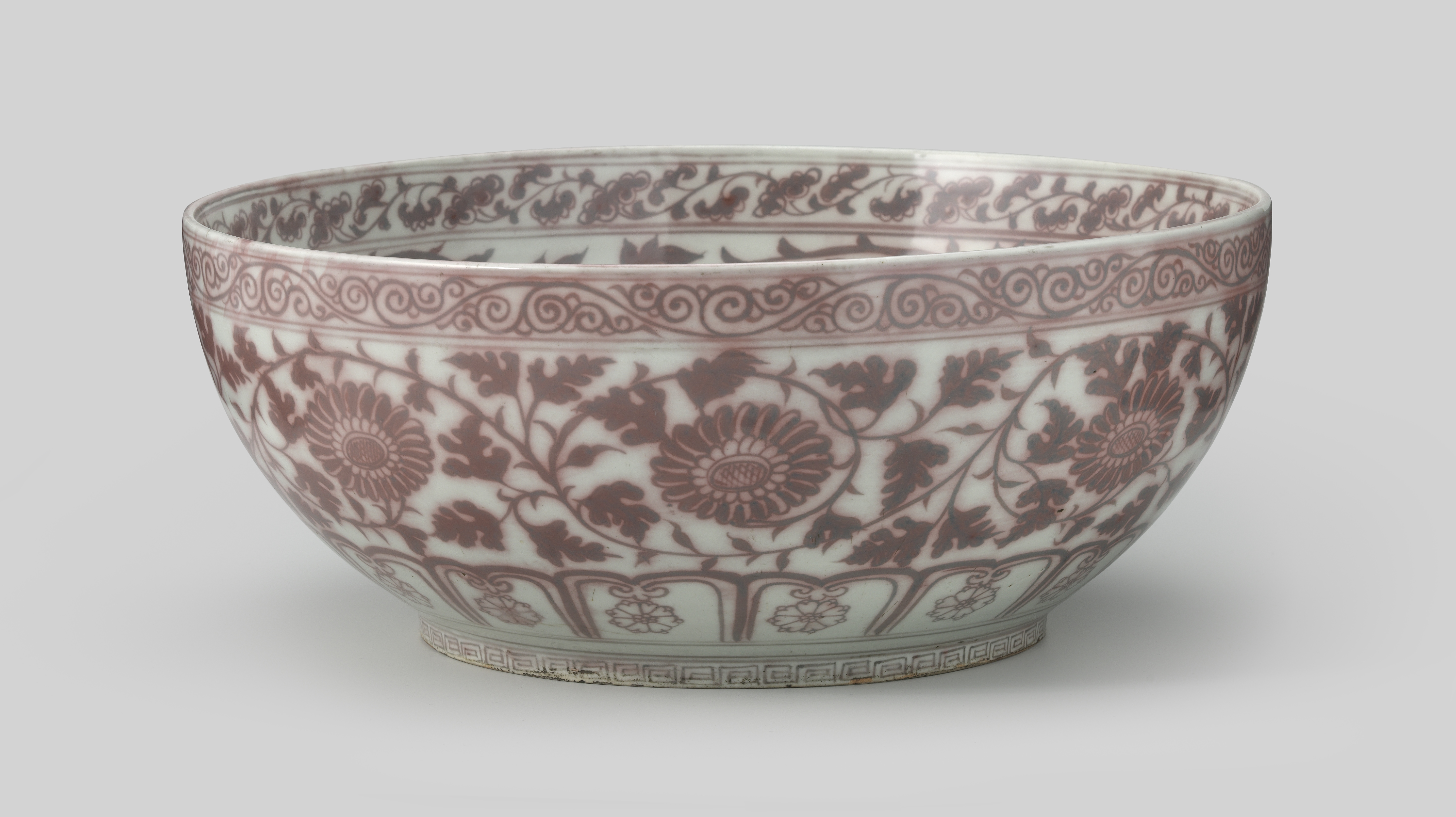
3) Kiln atmosphere
The kiln atmosphere depends on the amount of oxygen in the air inside the kiln during firing. There are three types of atmospheres: reduction, neutral or oxidation. A lot of air inside the kiln means there is a lot of oxygen and this is known as an oxidation atmosphere. But if the air circulates poorly, the fire becomes smoky and oxygen levels are lower, which is referred to as a reduction atmosphere. The atmosphere affects the colour and hardness of the ceramics and the glaze, so being able to control it is vital.
Glaze
Glaze is actually a thin layer of glass. The main component of glass is silica. The melting point of silica is much higher than the temperature of the kiln, which means a so-called flux must be added to the glaze mixture to lower the melting point. The different glazes are named after the type of flux used for them, such as lead glaze, alkaline lime glaze, and porcelain glaze (for which porcelain stone is used). The composition of the glaze affects its colour, its texture (e.g., oily, sugary, etc.), and at what temperature it can be fired.
Glazes can be coloured by pigments, but the final colour of these pigments after firing depends on the kiln atmosphere. For example, iron pigments produce cooler colours when reduced and warmer colours when oxidised, and the distinctive light-blue colour of so-called qingbai porcelain (fig. 6) results from the reduction atmosphere in which the iron-based glaze is fired.
During the firing of glazed ceramics, it is important that no ash or other dirt can either contaminate or adhere to the glaze. Objects were therefore placed in the kiln in protective cassettes (this is no longer necessary in today’s gas kilns). These cassettes are also useful for stacking objects on top of each other so that the kiln can be filled as efficiently as possible. To ensure that the object does not stick to the bottom of the cassette or the kiln, kiln furniture such as spurs (a kind of stilt) can be used. These are tapped off after firing, leaving so-called spur marks in the glaze (fig. 7). Objects can also be fired directly on the footrim or mouthrim, but then this part needs to remain unglazed. Sometimes a metal (usually copper) band (fig. 8) was added to the mouthrim after firing to disguise the unglazed part.
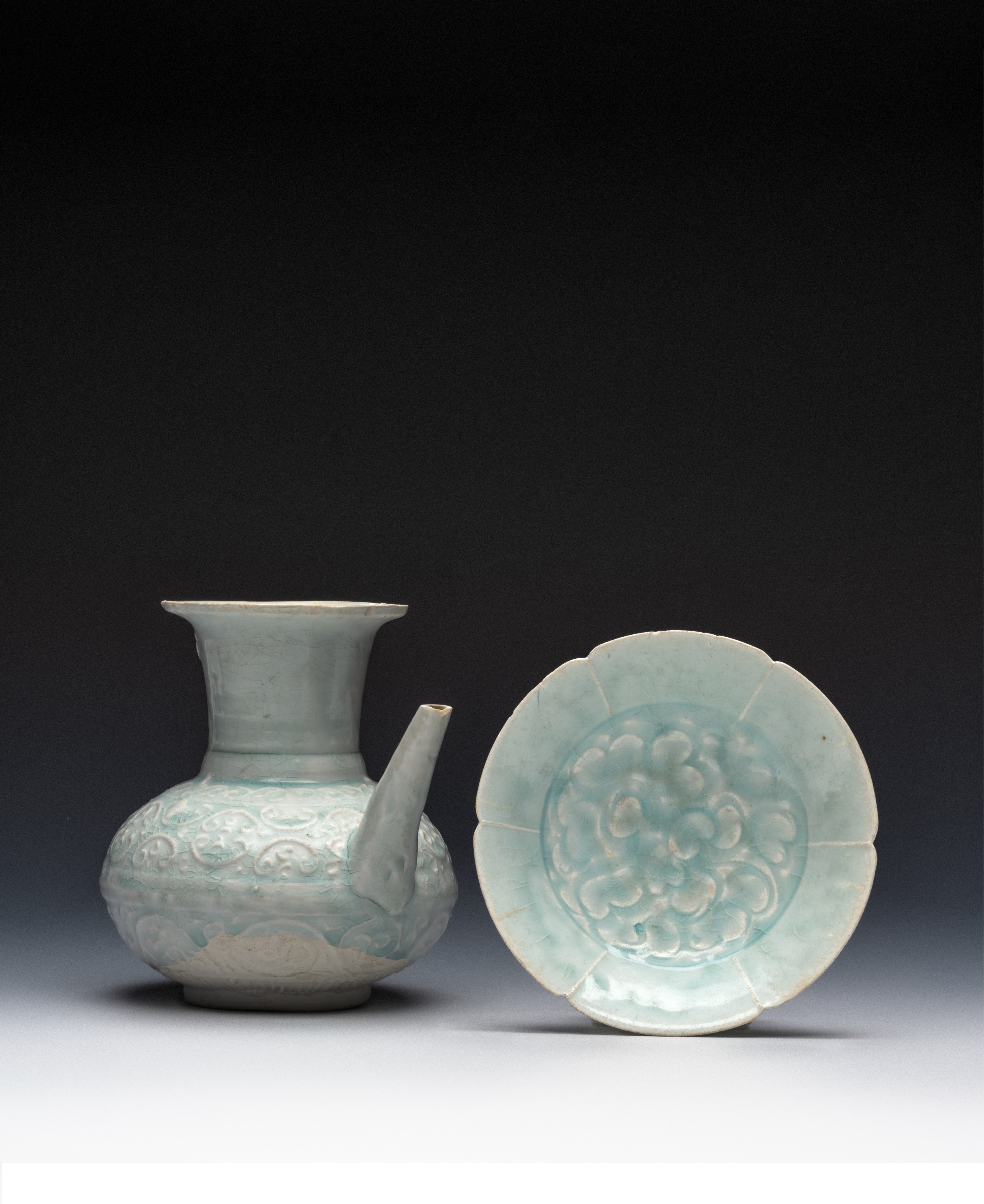
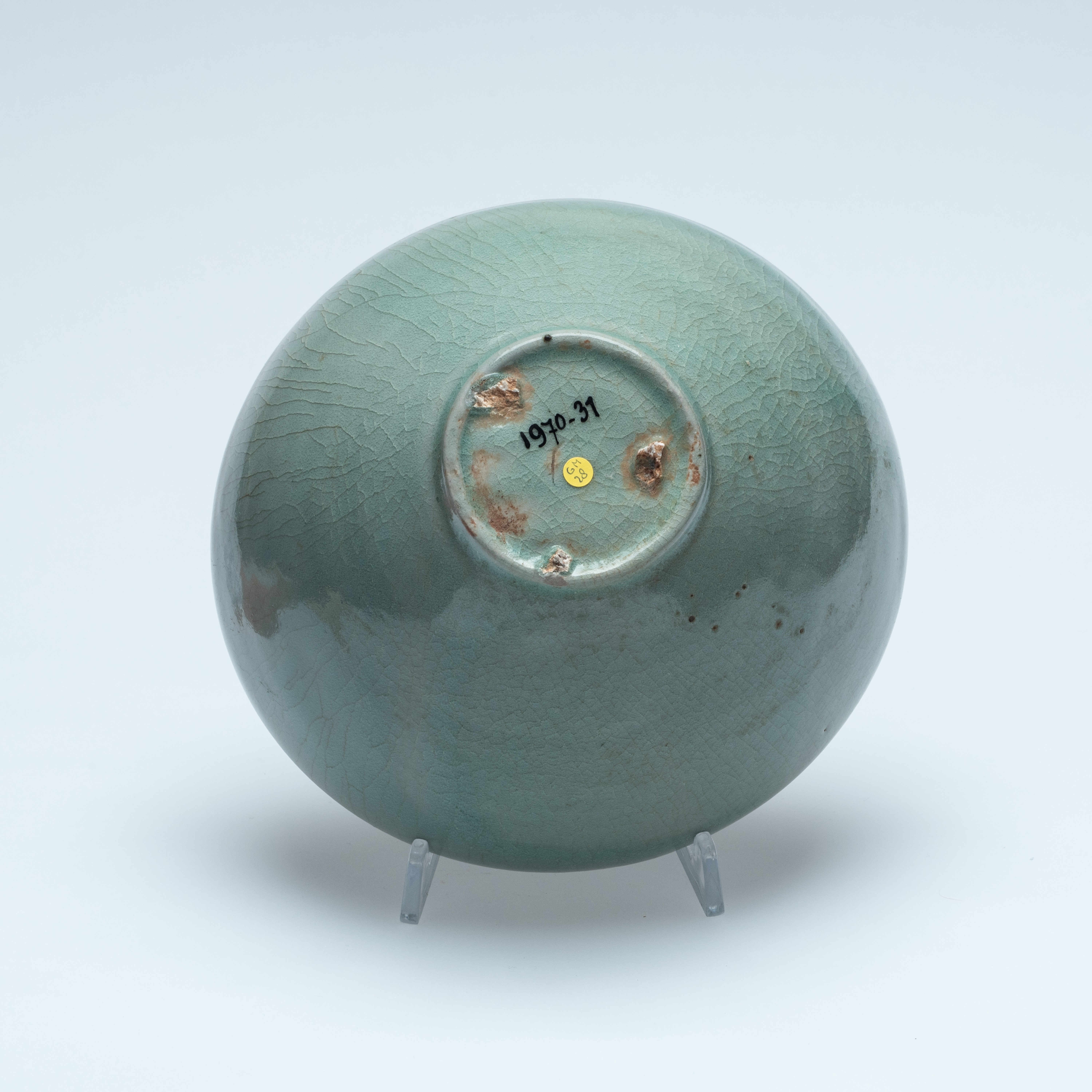
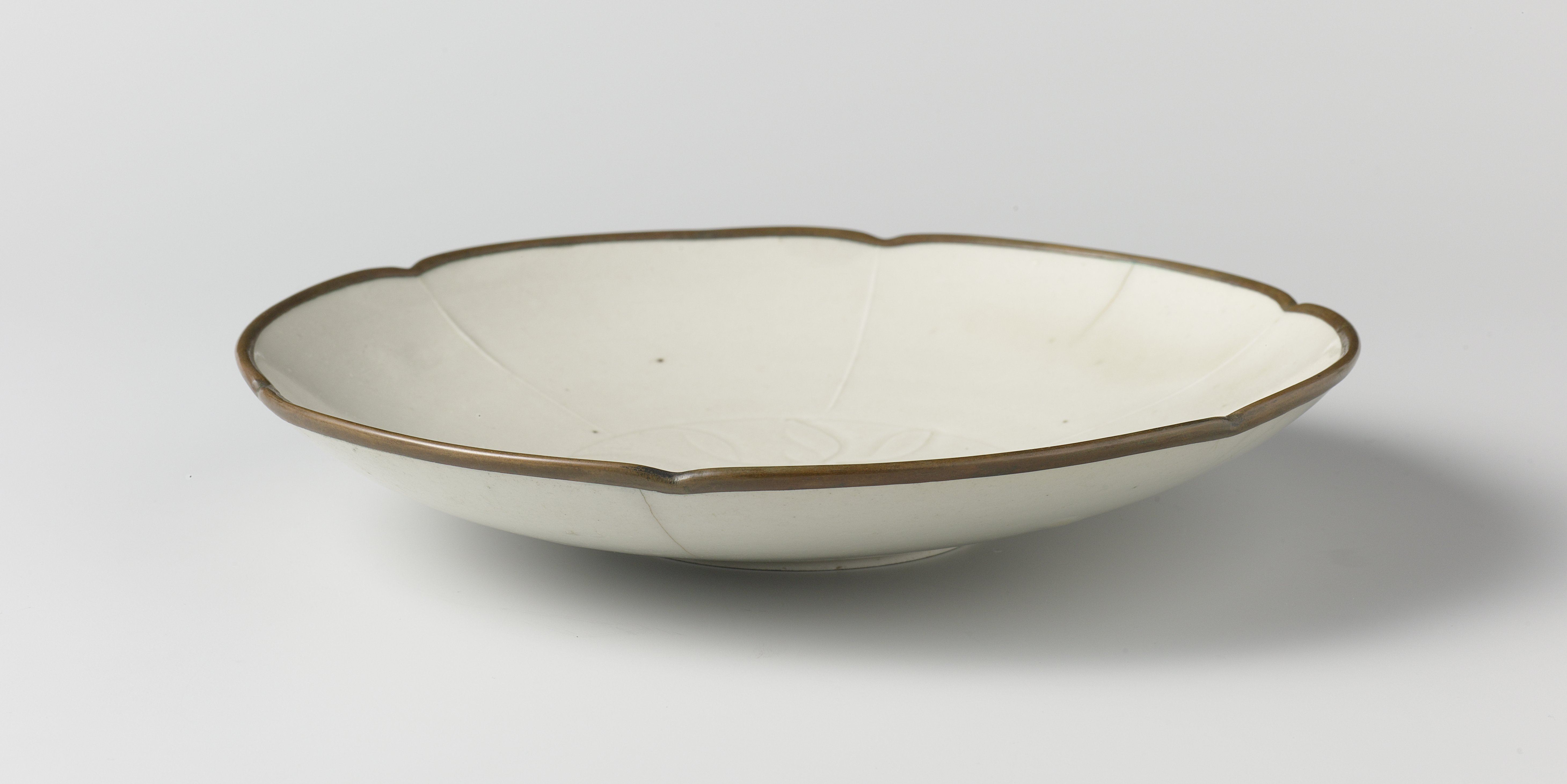
4) Decorative techniques
There are several ways of decorating porcelain that largely determine an object’s ultimate look. Many decorative techniques applied before glazing create a form of relief. This relief can be emphasised by the glaze (see also fig. 6 above). The glaze becomes thicker and thus darker where deeper incisions have been made in the clay and thinner where the clay has been raised. Relief can be applied by carving (into the dried, leather-hard clay), with a mould, with slip, or with appliqué. Furthermore, decorations can be applied with pigment prior to glazing, resulting in underglaze decorations. As indicated earlier, due to the high firing temperature, only cobalt, copper and iron pigments can be used for underglaze decorations on porcelain. Because copper and iron react less predictably, cobalt, which turns blue after firing, was preferred. Therefore, the vast majority of underglaze porcelain is blue-and-white.
Decorations can also be applied in the glaze (fig. 9), for example by sprinkling copper oxide onto the still unfired glaze. Another technique is placing papercuts and the leaves of trees (fig. 10) in the glaze. These burn away during the firing process, but leave a trace (like an X-ray) in the glaze. The glaze itself can also be the decoration, such as monochrome coloured glazes. It is also possible to manipulate the glaze in certain ways: for example, firing it at a slightly lower temperature than its melting point, so that it does not melt completely, resulting in an oily look.
Overglaze (also called enamel) decorations (fig. 11) can be applied after the glazed object has been fired. Depending on the pigments/composition, it has to be fired several more times, as not every pigment can withstand the same kiln temperature.
If the composition of the clay is incompatible with the composition of the glaze, the ‘glaze fit’ is not good. The clay body and the glaze can shrink and expand at different rates during firing, producing cracks in the glaze that may cause it to flake off. Sometimes this mismatched ‘glaze fit’ is deliberately exploited to achieve a decorative crackle effect (fig. 12).
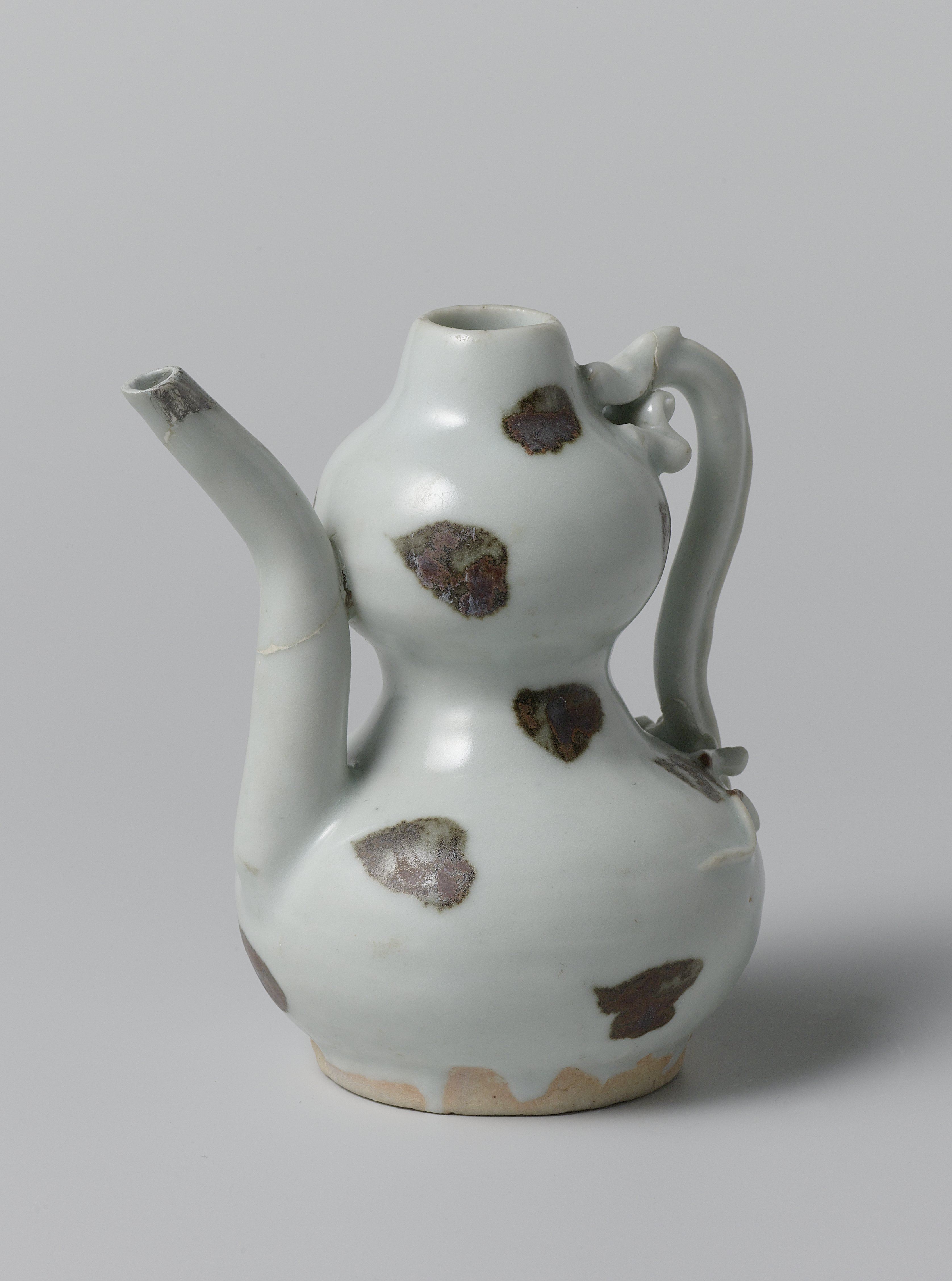
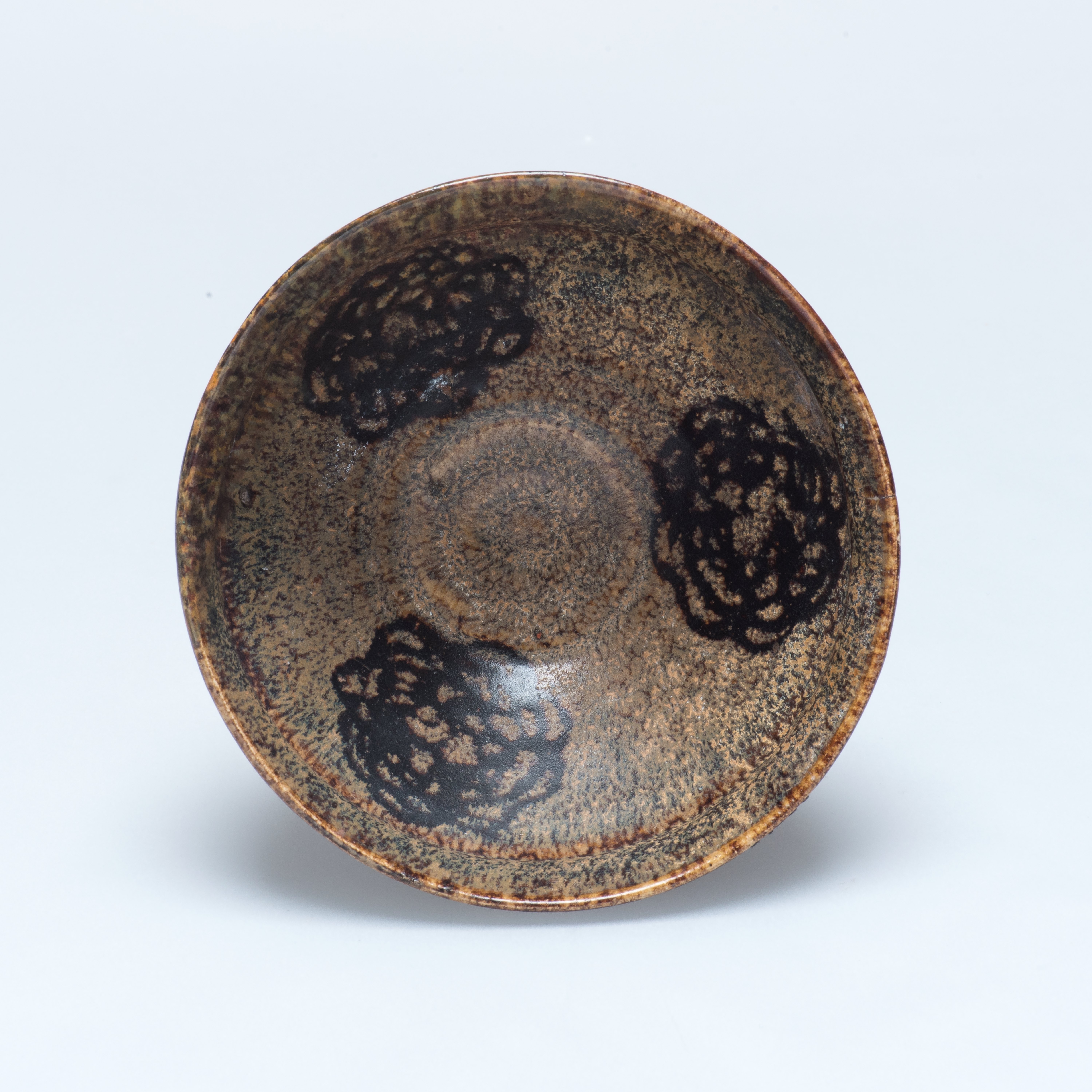
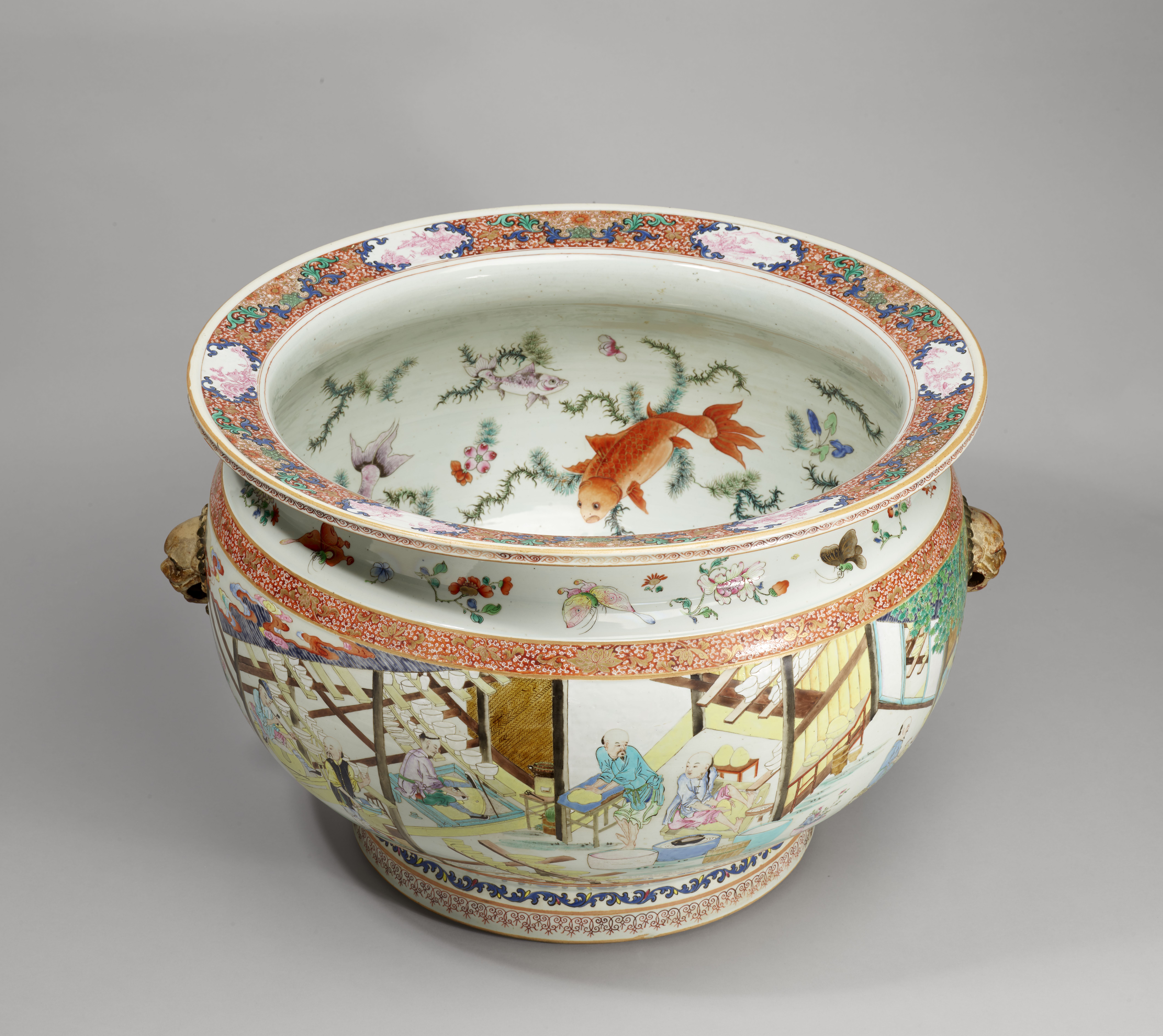
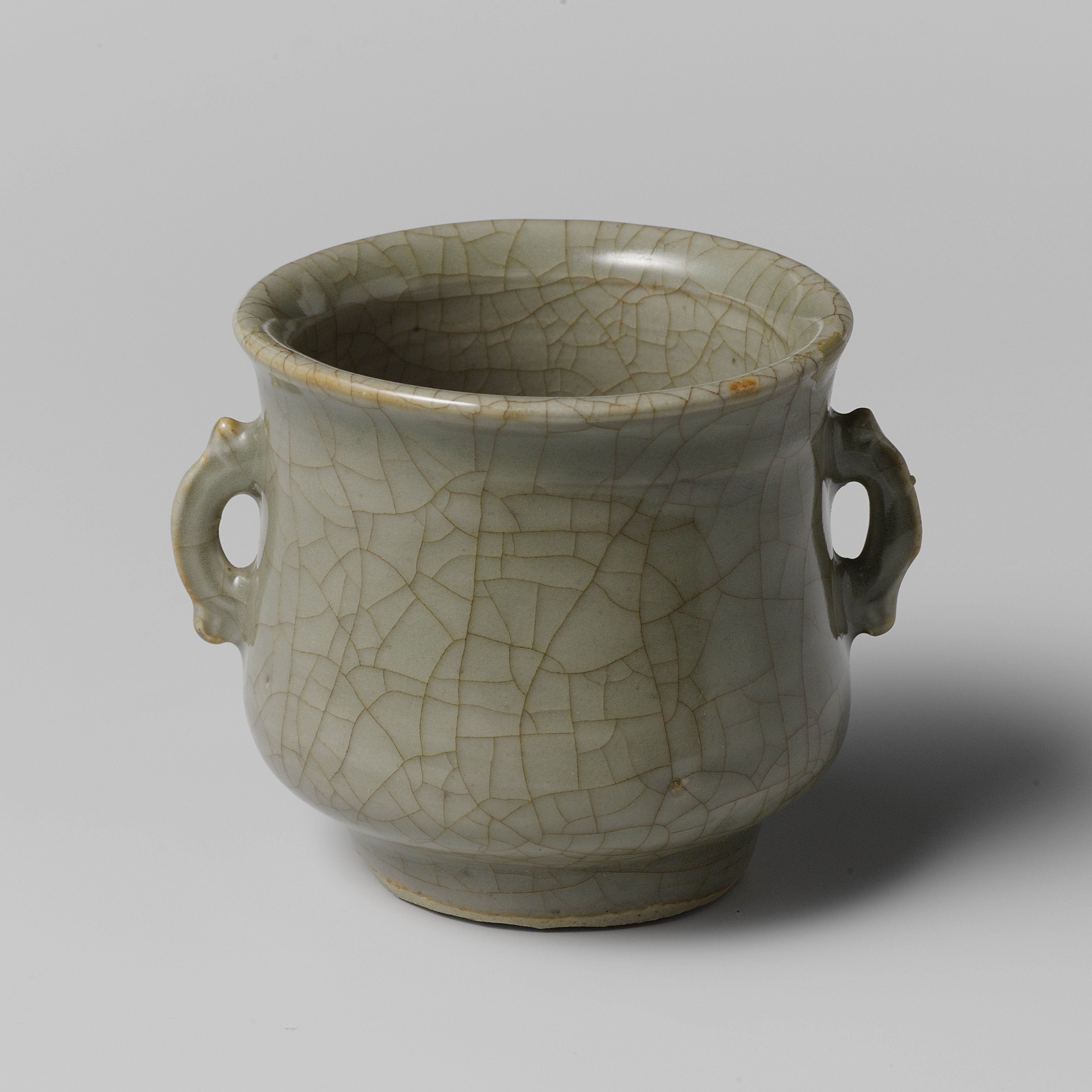
The manufacturing process
The sequence of making porcelain objects generally consists of the following steps:
- Clay preparation (quarrying, washing, sieving, kneading)
- Shaping the clay (on a wheel, in a mould, and/or by hand)
- Underglaze decoration (painting or creating relief)
- Glazing
- Firing
- Overglaze decoration
- Firing again
The steps in bold are essential, the others optional. A similar sequence is followed to make earthenware and stoneware, although the order may vary somewhat because the composition of the material is so different. When unglazed clay is fired it is called ‘biscuit’.
Making ceramics is a process of trial and error. Something can go wrong with every firing and small changes to the composition of the clay or glaze can have major consequences. Firing mistakes occur frequently and anyone walking through the kiln area of Jingdezhen will hear the clatter of many misfired objects being smashed to pieces. If we are aware of all these factors that influence the final product – and all the risks of failure along the way– we can appreciate the ceramic objects that have successfully emerged from the kilns with all the more admiration.
Literature
Kerr, Rose & Nigel Wood, Ceramic Technology, vol. 5, part 12, of Science and Civilisation in China, Cambridge, 2004.
Medley, Margaret The Chinese Potter, a Practical History of Chinese Ceramics. Phaidon, Oxford, 1976.
Pierson, Stacey, Earth, Fire and Water: Chinese Ceramic Technology, A Handbook for Non-specialists. Percival David Foundation, London, 1996.
Vainker, Shelagh, Chinese Pottery and Porcelain - From Prehistory to the Present. British Museum Press, 1991.
Wood, Nigel, Chinese Glazes: Their Origins, Chemistry, and Recreation, Philadelphia, 1999.